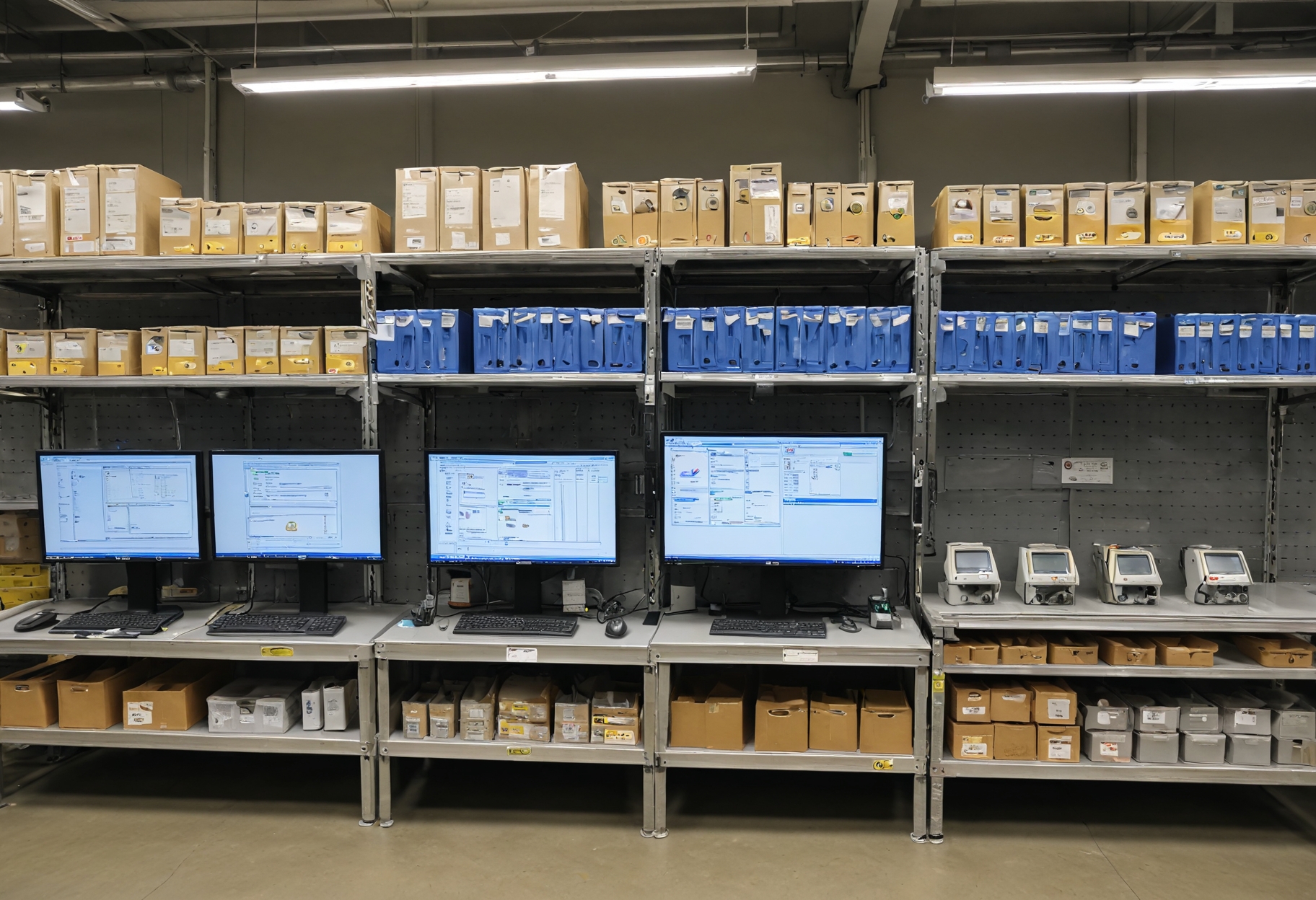
The Importance of Inventory Optimization in Warehouse Management
Efficient inventory management is a cornerstone of successful warehouse operations. Overstocking and stockouts are costly, impacting customer satisfaction, storage expenses, and cash flow. Digitized product tracking offers a solution by providing real-time visibility, predictive insights, and streamlined inventory workflows. Through digitization, warehouses can optimize inventory levels, improve accuracy, and ensure that products are available precisely when needed, maximizing efficiency and profitability.
How Digitized Product Tracking Optimizes Warehouse Inventory
- Real-Time Inventory Visibility Digitized product tracking allows warehouse managers to monitor stock levels in real time, gaining a clear view of product locations, quantities, and movements. This visibility reduces the risk of stock discrepancies, ensuring that data is always accurate and up-to-date, which improves inventory planning and responsiveness.
- Automated Reordering and Restocking With digital tracking, warehouses can set reorder points for each product. Automated alerts notify teams when stock levels fall below a certain threshold, ensuring that inventory is replenished just in time. This automation helps avoid both overstocking and stockouts, maintaining optimal inventory levels without excessive manual intervention.
- Improved Demand Forecasting Digitized systems collect historical and real-time sales data, helping warehouses forecast demand more accurately. By analyzing trends and predicting future needs, warehouses can adjust inventory levels based on seasonal patterns, promotional events, or market shifts, reducing excess stock and missed sales opportunities.
- Enhanced Space Utilization and Organization Digital tracking systems optimize storage allocation by analyzing product dimensions, demand frequency, and handling requirements. This optimization allows warehouses to allocate space more efficiently, minimizing wasted space and ensuring that high-demand products are easily accessible, which speeds up order fulfillment.
- Reduced Labor Costs through Automation Digitized product tracking automates processes such as inventory counting, reordering, and product locating, reducing manual labor. This efficiency minimizes human error, lowers labor costs, and allows staff to focus on high-value tasks such as quality control, order accuracy, and customer service.
Stages of Inventory Optimization with Digitized Product Tracking
- Inventory Intake and Sorting During intake, digitized systems record product details, quantities, and storage locations, ensuring that each item is properly categorized and tracked. Automated data entry reduces errors in initial inventory counts, setting the foundation for accurate inventory management.
- Dynamic Stock Monitoring and Reorder Alerts Digitized tracking systems continuously monitor stock levels, triggering reorder alerts when quantities reach predefined minimums. This real-time monitoring ensures that inventory remains at optimal levels, reducing the likelihood of shortages and overstock situations.
- Demand-Driven Inventory Adjustments Based on demand patterns and sales data, digital tracking allows warehouses to adjust inventory levels dynamically. By aligning stock quantities with actual demand, warehouses can prevent excess inventory, improve cash flow, and reduce holding costs.
- Order Fulfillment and Inventory Updates Digitized systems streamline the order fulfillment process by guiding workers to product locations, updating inventory records automatically as items are picked. This integration ensures accurate inventory counts and minimizes discrepancies, improving order accuracy and reducing fulfillment time.
Use Case Examples
- E-commerce Fulfillment: Reducing Stockouts with Automated Reordering An e-commerce fulfillment center used digitized product tracking to automate reordering for its high-demand products. By setting reorder points and real-time alerts, the center reduced stockouts by 30%, ensuring popular items were consistently available and improving customer satisfaction.
- Retail Distribution: Optimizing Space and Reducing Overstock A retail distribution warehouse implemented digitized tracking to monitor seasonal demand fluctuations and optimize inventory levels. By adjusting stock based on historical data, the warehouse reduced overstock by 25%, freeing up space and minimizing storage costs.
- Pharmaceutical Warehouse: Enhancing Accuracy and Compliance A pharmaceutical warehouse used digitized tracking to maintain accurate stock records for temperature-sensitive products. Automated alerts helped the warehouse avoid expiration-related waste, reducing stock discrepancies by 40% and ensuring compliance with industry regulations.
Analytics: Measuring the Impact of Digitized Product Tracking on Inventory Optimization
- Reduction in Stock Discrepancies Companies implementing digitized tracking systems experience up to a 40% reduction in stock discrepancies, leading to improved inventory accuracy and streamlined operations.
- Decrease in Stockouts and Overstocking With real-time monitoring and automated reordering, warehouses see a 25-30% reduction in stockouts and overstocking, which reduces lost sales and excess holding costs.
- Improvement in Order Fulfillment Speed By optimizing storage allocation and product accessibility, digitized tracking enables a 20-25% increase in order fulfillment speed, enhancing customer satisfaction and operational efficiency.
Conclusion: Digitized Product Tracking as a Solution for Efficient Inventory Management
Digitized product tracking transforms warehouse inventory management by improving visibility, automating processes, and optimizing stock levels. By reducing stock discrepancies, preventing stockouts, and enhancing space utilization, digital tracking systems enable warehouses to operate more efficiently and cost-effectively. For companies seeking a competitive advantage in logistics, digitized product tracking is a vital tool for maximizing productivity and meeting customer demands with precision.