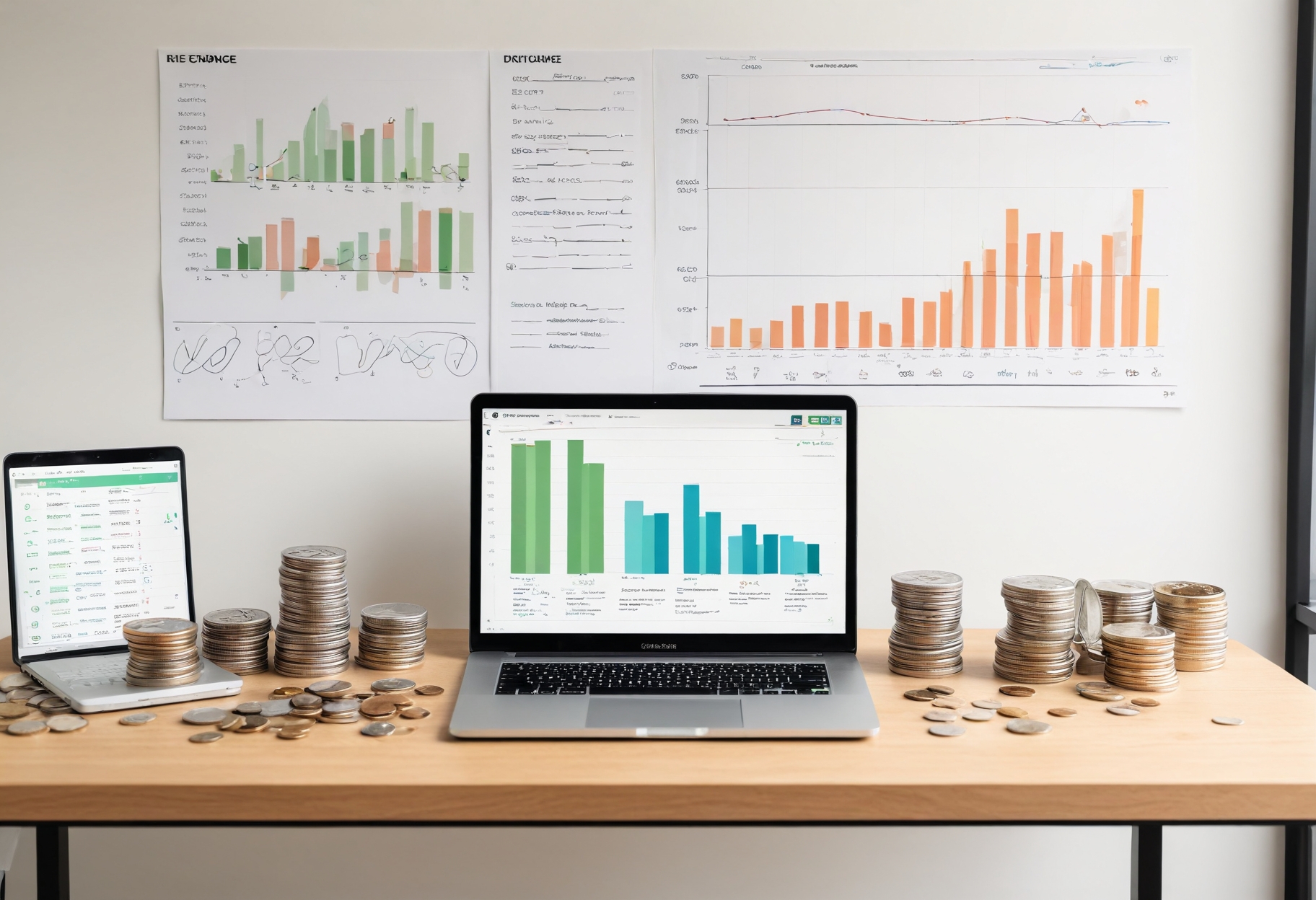
The Cost-Saving Potential of Digital Lifecycle Automation
Operational costs can add up quickly in product lifecycle management, particularly when tasks are repetitive, labor-intensive, and prone to human error. Digital lifecycle automation offers a solution by streamlining these routine tasks through advanced software and robotics, allowing companies to reduce manual effort and cut costs. By automating critical processes, organizations not only reduce expenses but also improve accuracy, increase productivity, and enhance responsiveness across the product lifecycle.
How Digital Automation Reduces Operational Costs
- Streamlined Inventory Management with Automated Reordering Automated inventory systems track stock levels in real-time and trigger reorder alerts or place orders automatically when inventory reaches predefined thresholds. This approach minimizes excess inventory, reduces holding costs, and ensures that materials are available exactly when needed, optimizing cash flow.
- Automated Quality Control for Consistent Standards Digital automation in quality control, using technologies like IoT sensors and AI-driven inspections, ensures that products meet quality standards without manual checks. This automation reduces labor costs, minimizes inspection errors, and allows companies to maintain high quality without added overhead.
- Optimized Compliance Tracking and Reporting Automated compliance tracking systems continuously monitor production standards and regulatory adherence, automatically generating reports for audits. By reducing the need for manual compliance checks, companies save on labor costs, reduce compliance risks, and simplify the audit process.
- Accelerated Production Scheduling and Resource Allocation Automation tools optimize production schedules and allocate resources efficiently based on demand forecasts and real-time data. By reducing downtime and maximizing resource utilization, companies minimize production delays, reduce idle time, and cut costs associated with underutilized equipment and labor.
- Enhanced Document Management and Record-Keeping Digital lifecycle automation includes automated document management, which organizes and maintains records, including design files, quality certifications, and compliance reports. This streamlined document handling saves time and reduces costs associated with manual paperwork, enabling faster access to critical information.
Use Case Examples
- Manufacturing: Reducing Labor Costs with Automated Quality Checks A manufacturing company implemented automated quality control using AI-powered cameras and IoT sensors. By replacing manual inspections with automated checks, the company reduced labor costs by 30% and minimized product defects, resulting in higher quality output and lower rework costs.
- Retail: Optimizing Inventory with Automated Reordering Systems A retail chain used automated reordering software to manage inventory based on real-time sales data. The automation reduced excess stock by 25%, cut down storage costs, and ensured popular products were consistently available, improving customer satisfaction and operational efficiency.
- Healthcare: Lowering Compliance Costs with Automated Documentation A healthcare equipment manufacturer adopted automated compliance tracking and documentation systems. By automating the preparation and filing of regulatory documents, the company saved 20% on compliance costs and reduced the risk of non-compliance, making audits faster and more reliable.
Analytics: Measuring the Impact of Digital Automation on Operational Costs
- Reduction in Labor Costs Companies implementing digital lifecycle automation report a 20-30% reduction in labor costs, as routine tasks are automated, freeing up employees to focus on higher-value activities.
- Decrease in Inventory Holding Costs Automated inventory management reduces excess stock and cuts holding costs by 15-25%, as real-time tracking aligns inventory levels with actual demand.
- Improvement in Production Efficiency Automated scheduling and resource allocation enhance production efficiency by 20-30%, as automation minimizes downtime, maximizes resource utilization, and accelerates workflows.
Conclusion: Digital Automation as a Path to Cost Efficiency in Lifecycle Management
Digital lifecycle automation is a powerful cost-saving tool that streamlines processes, reduces errors, and optimizes resource use. By automating routine tasks in inventory management, quality control, compliance, and documentation, companies can lower operational costs and enhance productivity. For organizations seeking greater efficiency and cost control, implementing digital automation within the product lifecycle offers a strategic advantage for maintaining profitability and supporting sustainable growth.