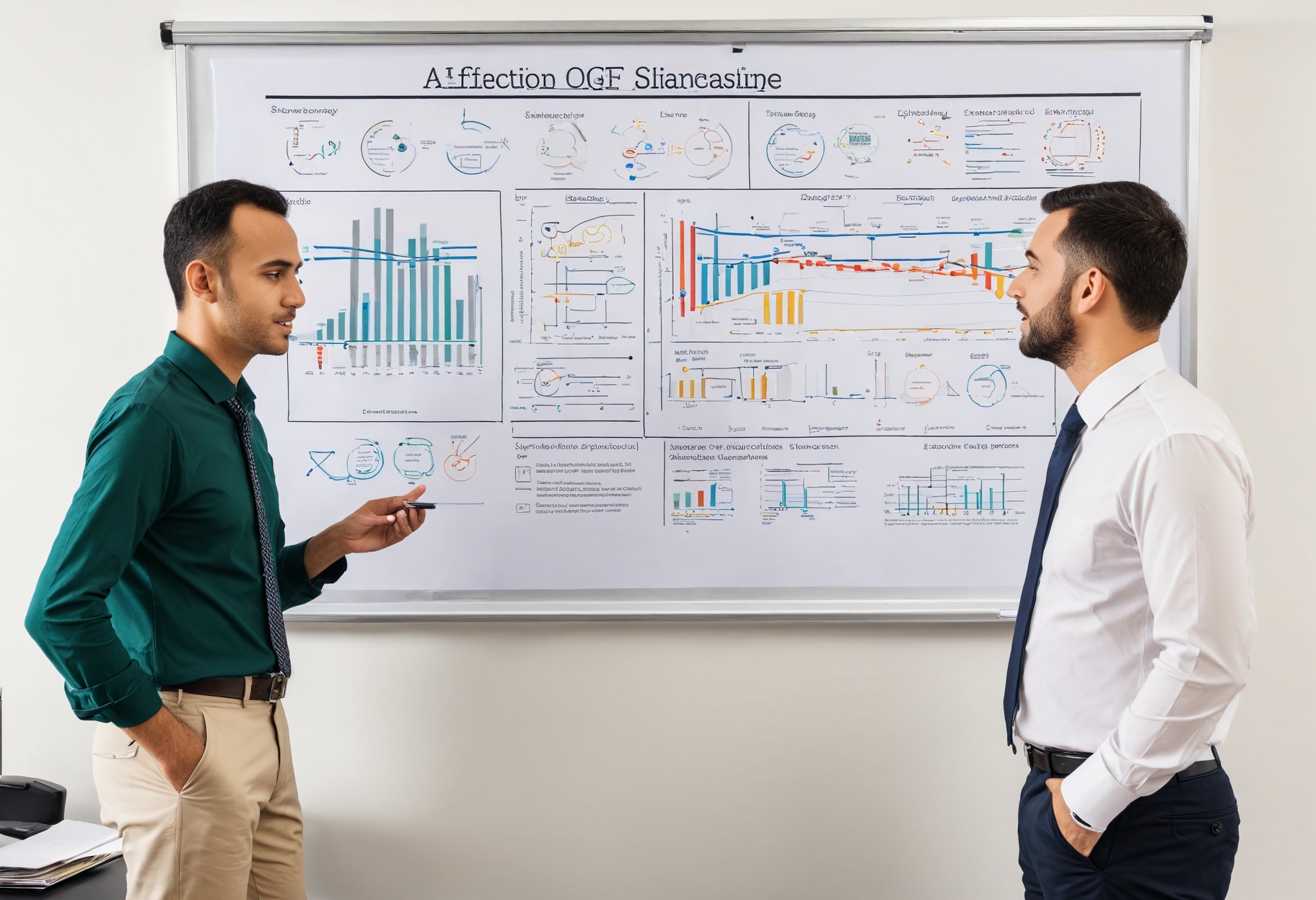
The Need for Flexible Resource Allocation in PLM
Efficient resource allocation is crucial for maintaining smooth operations across the product lifecycle. However, fixed resource plans can be limiting when market conditions, demand, or production schedules change unexpectedly. Dynamic resource allocation provides a flexible approach, allowing companies to adjust resource distribution in real time based on actual needs and data insights. By embracing dynamic allocation, companies can respond more effectively to fluctuations, optimize resource use, and achieve better control over lifecycle management.
How Dynamic Resource Allocation Enhances Product Lifecycle Management
- Real-Time Data for Informed Resource Adjustments Digital PLM tools provide real-time visibility into production demands, inventory levels, and workforce availability. This data enables managers to make informed decisions, reallocating resources as needed to meet current production goals, avoid bottlenecks, and prevent resource shortages.
- Enhanced Agility with Automated Resource Scheduling Automated scheduling systems dynamically adjust work shifts, material orders, and equipment use based on demand fluctuations. This automation reduces manual adjustments, improves agility, and ensures that resources are aligned with actual production needs, reducing downtime and enhancing operational efficiency.
- Optimized Material Usage and Inventory Management Dynamic allocation allows companies to align materials with production schedules, minimizing excess inventory and reducing material waste. By adjusting material orders based on real-time demand and usage rates, companies can reduce holding costs, optimize space, and prevent overproduction.
- Flexible Workforce Management Real-time workforce data enables companies to allocate labor efficiently by adjusting shift schedules or reallocating team members based on production requirements. This flexibility ensures that labor resources are used effectively, minimizing idle time and supporting a more responsive production environment.
- Cost Control through Demand-Based Resource Allocation By dynamically adjusting resources according to demand, companies can avoid overcommitting resources and incurring unnecessary costs. This demand-based approach reduces expenses associated with excess labor, materials, and equipment, supporting a lean, cost-effective lifecycle.
Use Case Examples
- Automotive: Reducing Downtime with Real-Time Resource Adjustments An automotive manufacturer used dynamic resource allocation to adjust labor and equipment based on production line needs. Real-time insights allowed the company to prevent bottlenecks by reallocating resources during peak demand, reducing downtime by 20% and maintaining consistent output.
- Consumer Goods: Optimizing Inventory Levels for Seasonal Demand A consumer goods company implemented dynamic resource allocation to manage seasonal demand fluctuations. By adjusting material orders and labor based on forecasted demand, the company reduced excess inventory by 25% and optimized storage space, leading to significant cost savings.
- Healthcare: Improving Workforce Flexibility for Production Demands A healthcare equipment manufacturer used dynamic scheduling to align workforce resources with changing production needs. By reallocating labor in real time, the company improved productivity by 30% during high-demand periods, ensuring timely delivery and maintaining quality standards.
Analytics: Measuring the Impact of Dynamic Resource Allocation on Lifecycle Efficiency
- Reduction in Idle Time and Downtime Companies using dynamic resource allocation report a 20-30% reduction in idle time and downtime, as real-time adjustments ensure that resources are consistently aligned with production needs.
- Decrease in Inventory Holding Costs By optimizing material orders and reducing excess inventory, businesses experience a 15-25% decrease in holding costs, as inventory levels are matched closely with demand.
- Increase in Workforce Productivity Real-time workforce adjustments lead to a 20-30% increase in productivity, as labor resources are allocated efficiently based on real-time requirements, supporting a streamlined production process.
Conclusion: Dynamic Resource Allocation as a Driver of Efficiency and Agility
Dynamic resource allocation is essential for companies aiming to maintain efficiency, cost control, and responsiveness across the product lifecycle. By leveraging real-time data, automated scheduling, and flexible resource management, companies can optimize labor, materials, and equipment to meet demand effectively. For organizations focused on agility and operational excellence, adopting dynamic resource allocation in PLM offers a practical solution to navigate changing conditions and maintain high performance.