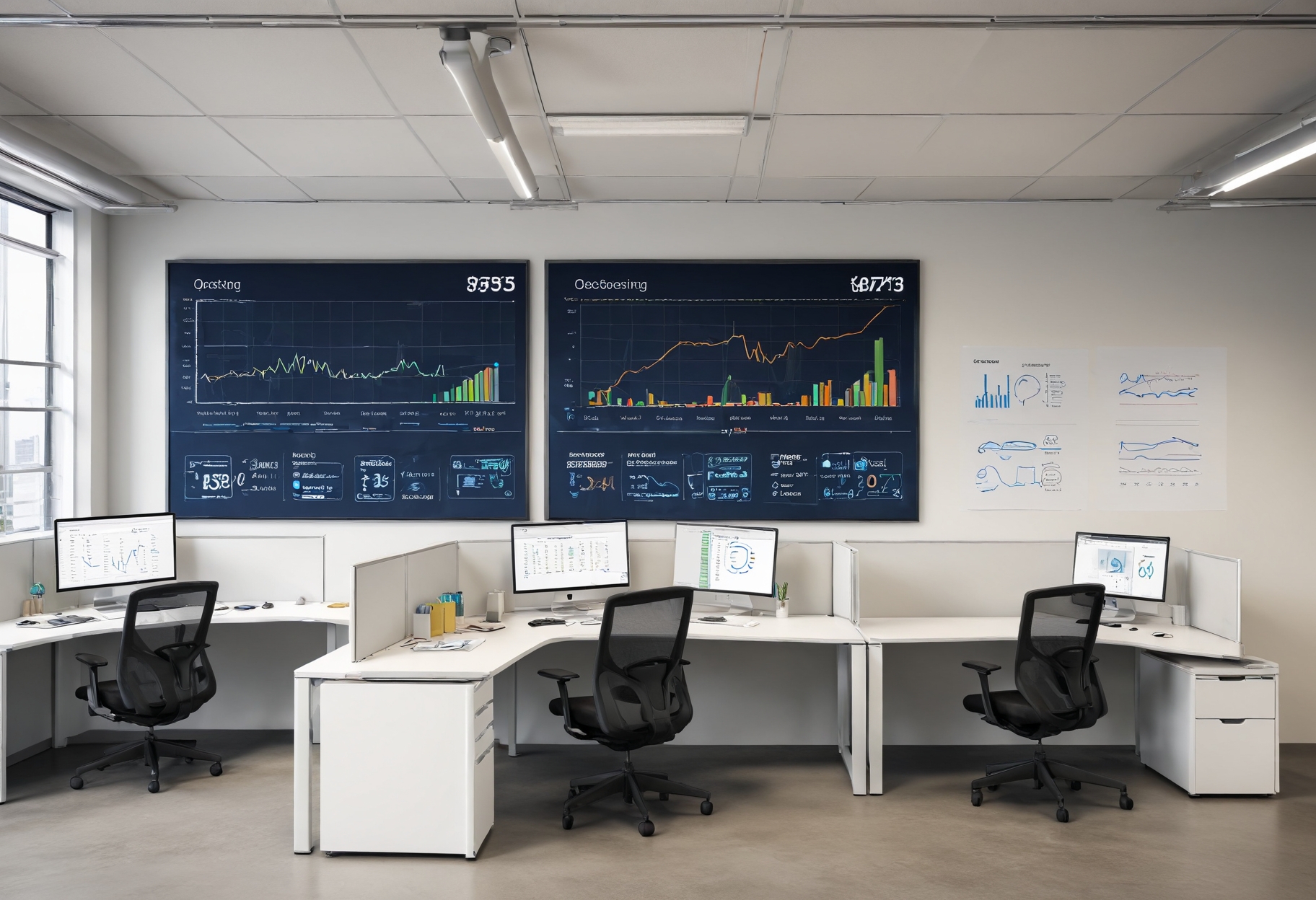
The Role of Procurement in Product Lifecycle Management
Procurement is a critical aspect of product lifecycle management that directly impacts production timelines, costs, and overall efficiency. However, traditional procurement methods can be slow, manual, and prone to errors, affecting the availability of materials and the reliability of suppliers. Digital lifecycle tools streamline procurement by automating sourcing tasks, providing real-time visibility into supplier performance, and enhancing decision-making. With digital procurement, companies can optimize supplier relationships, reduce delays, and maintain a steady supply chain.
How Digital Lifecycle Tools Improve Procurement Efficiency
- Automated Sourcing and Supplier Management Digital lifecycle tools automate routine sourcing tasks, such as vendor selection, price comparison, and contract management. This automation reduces the time needed to secure suppliers, allowing procurement teams to focus on strategic tasks and ensuring that material needs are met quickly and cost-effectively.
- Real-Time Data on Material Availability and Costs Digital tools provide real-time insights into material stock levels, market prices, and lead times. This visibility allows procurement teams to make informed decisions, adjust orders based on actual demand, and secure materials at the best possible price, improving inventory management and cost efficiency.
- Enhanced Supplier Collaboration and Communication Digital platforms facilitate communication between procurement teams and suppliers by providing a shared workspace for updates, order confirmations, and delivery tracking. This real-time collaboration reduces miscommunications, improves supplier relationships, and ensures that materials arrive on time to keep production on schedule.
- Risk Management Through Supplier Performance Tracking Digital lifecycle tools track supplier performance metrics, such as delivery reliability, quality consistency, and responsiveness. By monitoring these metrics, companies can identify high-performing suppliers, address potential risks, and make data-driven decisions to secure a reliable supply chain.
- Optimized Inventory Levels with Demand Forecasting Integration Many digital procurement tools integrate with demand forecasting systems, allowing teams to adjust orders based on projected demand. This integration minimizes the risk of overstocking or stockouts, improves cash flow, and aligns procurement with actual production needs, supporting a lean inventory approach.
Use Case Examples
- Manufacturing: Reducing Lead Times with Automated Sourcing A manufacturing company used digital lifecycle tools to automate sourcing and vendor selection. By reducing the time required to secure suppliers, the company decreased lead times by 25% and maintained a steady supply of materials, supporting uninterrupted production.
- Retail: Optimizing Inventory with Real-Time Material Insights A retail company adopted digital procurement tools to monitor stock levels and material costs in real-time. By aligning orders with current demand, the company reduced excess inventory by 20% and optimized storage costs, improving profitability.
- Pharmaceuticals: Enhancing Supplier Reliability with Performance Tracking A pharmaceutical company used digital lifecycle tools to track supplier performance, focusing on quality and delivery consistency. By identifying and collaborating with reliable suppliers, the company improved material quality, reduced delays by 30%, and ensured compliance with industry standards.
Analytics: Measuring the Impact of Digital Tools on Procurement Efficiency
- Reduction in Lead Times Companies using digital procurement tools report a 20-30% reduction in lead times, as automated sourcing and real-time communication improve supplier responsiveness and material availability.
- Decrease in Inventory Holding Costs With optimized inventory levels and demand-based ordering, businesses experience a 15-25% reduction in inventory holding costs, as stock is aligned with actual needs and minimized for efficiency.
- Improvement in Supplier Reliability Digital tools improve supplier reliability by 20-25%, as performance tracking, real-time updates, and automated tasks support stronger supplier relationships and reduce material-related delays.
Conclusion: Digital Tools as a Catalyst for Streamlined Procurement
Digital lifecycle tools transform procurement processes by automating sourcing, providing real-time data, and enhancing supplier collaboration. By improving inventory management, reducing lead times, and supporting proactive decision-making, digital tools optimize procurement efficiency across the product lifecycle. For companies focused on maintaining a reliable, cost-effective supply chain, implementing digital procurement solutions offers a strategic advantage for sustained operational success.