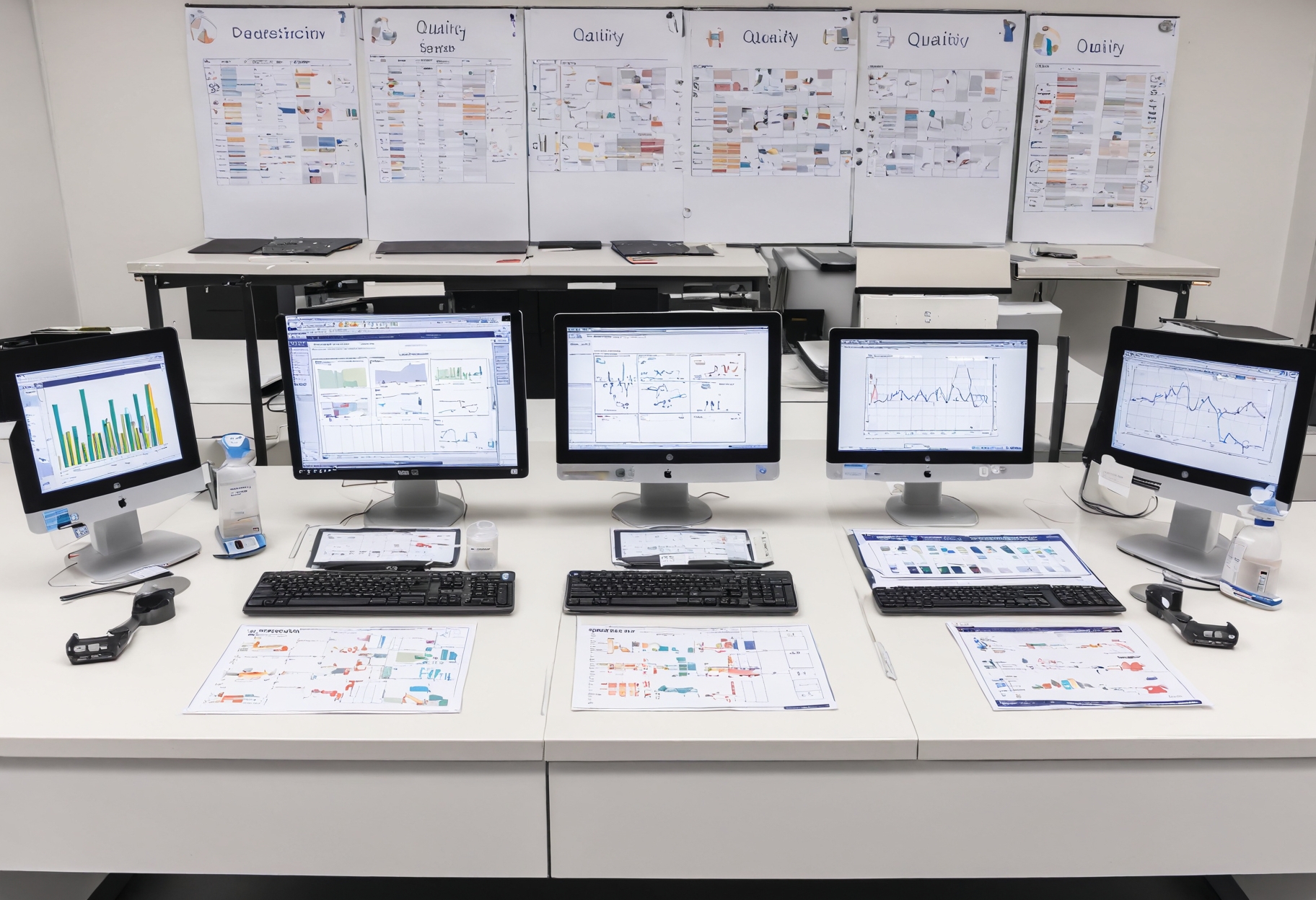
The Power of Digital Twins in Product Lifecycle Management
Digital twins provide a virtual counterpart to physical products, allowing teams to monitor and analyze asset performance in real time. By continuously collecting data from physical assets, digital twins enable teams to simulate, test, and refine products without disrupting operations. This advanced modeling technique optimizes each stage of the product lifecycle, from design to end-of-life, leading to better products, proactive maintenance, and data-driven decisions.
How Digital Twins Enhance Product Lifecycle Management
- Real-Time Monitoring and Data Collection Digital twins provide continuous monitoring of asset conditions, capturing data on performance metrics such as temperature, pressure, and usage patterns. This real-time data enables teams to detect anomalies early, reducing the risk of unexpected failures and allowing for quick adjustments.
- Predictive Maintenance and Reduced Downtime With predictive analytics capabilities, digital twins allow companies to forecast when maintenance is required based on actual asset conditions. This predictive approach minimizes unplanned downtime, reduces repair costs, and extends the lifecycle of equipment by addressing issues before they lead to breakdowns.
- Simulation of Design and Performance Scenarios Digital twins allow design teams to test new features, materials, and configurations virtually, reducing the need for physical prototypes. By simulating real-world conditions, companies can optimize designs, identify potential issues, and ensure products meet quality standards before production, saving time and resources.
- Enhanced Decision-Making with Predictive Insights The continuous data and analytics from digital twins provide insights into asset performance, lifecycle trends, and operational efficiency. With predictive insights, teams can make informed decisions regarding resource allocation, process improvements, and asset replacement, maximizing overall productivity.
- Improved End-of-Life and Sustainability Planning By analyzing usage data, digital twins can forecast the optimal time for asset replacement or disposal. This approach allows companies to plan end-of-life strategies that minimize waste, support recycling initiatives, and align with sustainability goals.
Use Case Examples
- Aerospace: Enhancing Aircraft Maintenance with Predictive Models An aerospace company used digital twins to monitor the performance of aircraft engines in real time. By analyzing data on temperature, vibration, and fuel consumption, the company predicted maintenance needs accurately. This proactive maintenance reduced unplanned downtime by 30% and extended engine lifespan.
- Manufacturing: Optimizing Equipment Efficiency on the Production Floor A manufacturing plant implemented digital twins for its high-value machinery, enabling virtual simulations of production processes. This approach allowed the company to optimize machine configurations, improve production speed, and reduce equipment downtime, resulting in a 25% increase in productivity.
- Energy: Extending the Life of Wind Turbines with Digital Twin Technology An energy provider used digital twins for its wind turbines, tracking metrics like blade speed, angle, and wear patterns. By predicting maintenance needs and optimizing turbine settings based on real-time conditions, the company extended turbine lifespan by 20% and improved energy efficiency.
Analytics: Measuring the Impact of Digital Twins on Product Lifecycle Management
- Reduction in Maintenance Costs Companies using digital twins for predictive maintenance report a 25-35% reduction in maintenance costs, as issues are addressed proactively, reducing the need for emergency repairs and part replacements.
- Increase in Design Efficiency By simulating designs virtually, companies achieve a 20-30% improvement in design efficiency, as digital twins allow for faster iteration cycles and minimize the need for physical prototyping.
- Improvement in Asset Utilization Rates With real-time monitoring and optimized maintenance, digital twins increase asset utilization rates by up to 25%, as assets experience fewer breakdowns and remain operational for longer periods.
Conclusion: Digital Twins as a Game-Changer for Lifecycle Management
Digital twins are transforming product lifecycle management by enabling real-time insights, predictive maintenance, and virtual simulations. By providing a digital counterpart to physical assets, digital twins help companies optimize design, reduce downtime, and make data-driven decisions. For organizations looking to maximize asset value and enhance lifecycle efficiency, implementing digital twins offers a cutting-edge approach to proactive management and continuous improvement.