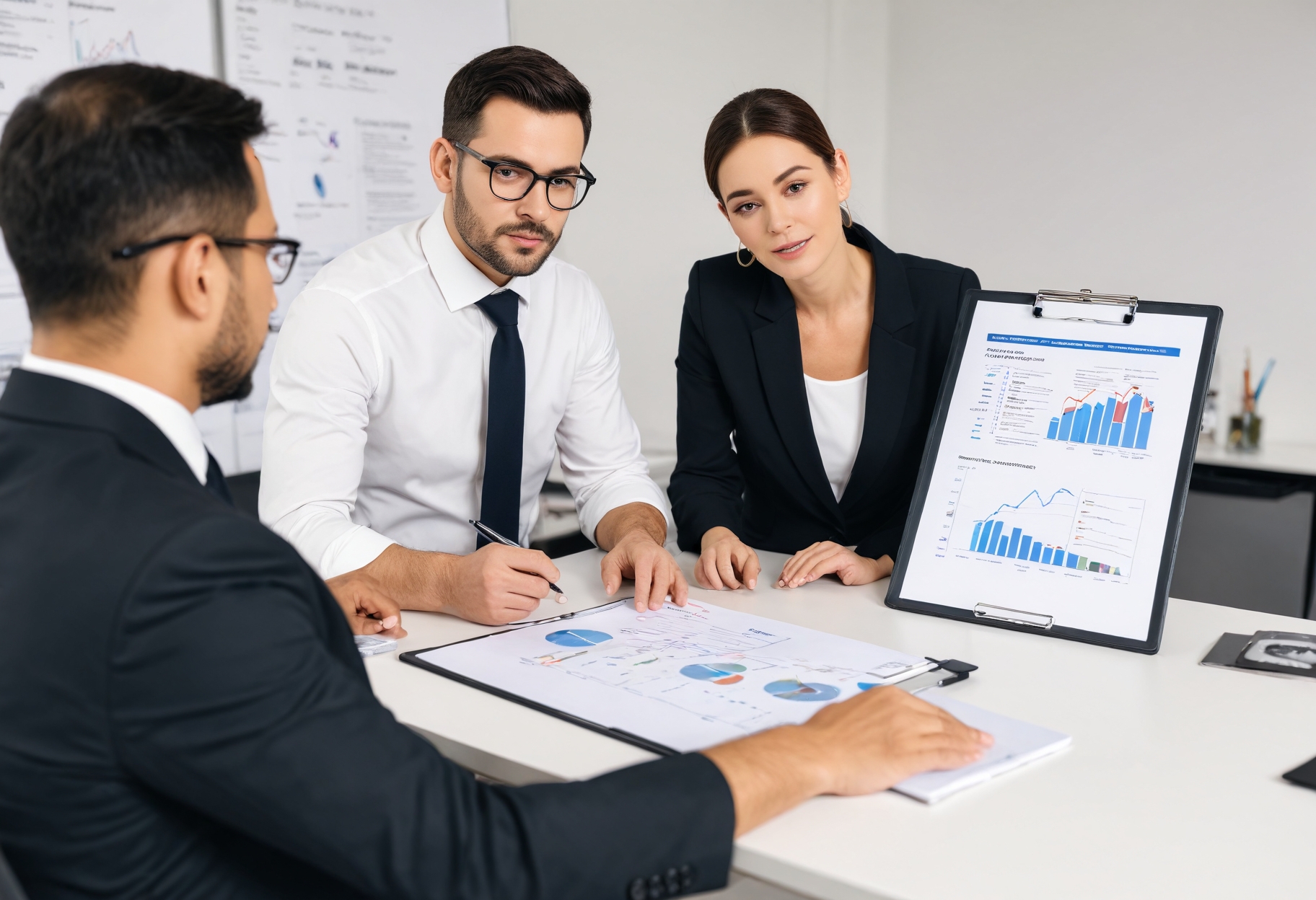
The Importance of Supplier Collaboration in Product Lifecycles
Supplier collaboration is critical for companies to meet production demands, ensure quality standards, and remain competitive. However, manual processes and fragmented communication can create delays, misunderstandings, and quality control challenges. Digital lifecycle tools provide a centralized platform for managing supplier relationships, tracking materials, and sharing real-time information, making procurement processes smoother and more efficient.
How Digital Lifecycle Tools Enhance Supplier Collaboration
- Centralized Data for Real-Time Access Digital lifecycle tools create a single source of truth where companies and suppliers can access updated product specifications, delivery schedules, and order statuses. This centralized access ensures that everyone is working with accurate, current information, reducing the likelihood of miscommunications and helping suppliers meet production needs.
- Automated Communication and Order Management By automating routine communication tasks such as order confirmations, shipping notifications, and inventory updates, digital tools streamline supplier interactions. This automation reduces the time spent on manual updates, enhances efficiency, and allows both parties to focus on high-value activities.
- Enhanced Visibility into Supplier Performance Lifecycle tools offer performance tracking metrics, enabling companies to monitor supplier reliability, delivery times, and quality consistency. This visibility helps companies identify high-performing suppliers, address issues proactively, and make data-driven decisions on supplier partnerships.
- Risk Management through Early Issue Detection With real-time tracking, companies can monitor supply chain risks—such as delivery delays or inventory shortages—as they arise. Automated alerts notify teams when issues occur, allowing for quick resolution and minimizing the risk of production disruptions or quality problems.
- Improved Alignment with Production Goals Digital lifecycle tools provide suppliers with up-to-date forecasts and production schedules, allowing them to adjust their production processes to meet demand more accurately. This alignment minimizes inventory holding costs, reduces waste, and ensures that supplies are available as production needs fluctuate.
Use Case Examples
- Automotive Industry: Reducing Lead Times with Supplier Alignment An automotive manufacturer used digital lifecycle tools to share real-time production forecasts with suppliers. This alignment allowed suppliers to adjust their manufacturing schedules based on actual demand, reducing lead times by 20% and minimizing production delays.
- Electronics Manufacturing: Improving Quality with Transparent Tracking An electronics company adopted digital lifecycle tools to monitor supplier quality in real-time. Automated alerts notified the company of any material quality deviations, allowing for immediate feedback to suppliers. This proactive approach improved material quality by 25%, reducing the need for post-production quality checks.
- Retail: Optimizing Inventory Management with Reorder Automation A retail chain implemented digital lifecycle tools to automate reorder points and stock replenishment with suppliers. Real-time stock monitoring allowed the company to avoid stockouts, reduce excess inventory, and improve cash flow by aligning orders more closely with consumer demand.
Analytics: Measuring the Impact of Digital Lifecycle Tools on Supplier Collaboration
- Reduction in Order Processing Time Companies using digital tools for supplier collaboration report a 25-30% reduction in order processing time, as automated updates and real-time data improve procurement efficiency.
- Decrease in Supply Chain Disruptions With proactive monitoring and automated alerts, businesses experience a 20-25% decrease in supply chain disruptions, as issues are identified early and resolved quickly.
- Improvement in Supplier Quality Consistency Digital tools improve quality consistency by 15-20%, as real-time tracking enables immediate feedback, helping suppliers adhere to quality standards more effectively.
Conclusion: Digital Lifecycle Tools as a Catalyst for Effective Supplier Collaboration
Digital lifecycle tools transform supplier collaboration by centralizing data, automating communication, and enhancing visibility. By streamlining procurement processes, reducing lead times, and improving quality standards, digital tools help companies build stronger, more productive relationships with suppliers. For organizations seeking to optimize supply chain performance, adopting digital lifecycle tools offers a path to better alignment, proactive issue management, and mutually beneficial partnerships.